เทคนิคการลดความสูญเสีย 7+1 ประการ 7+1 Wastes for Cost Reduction
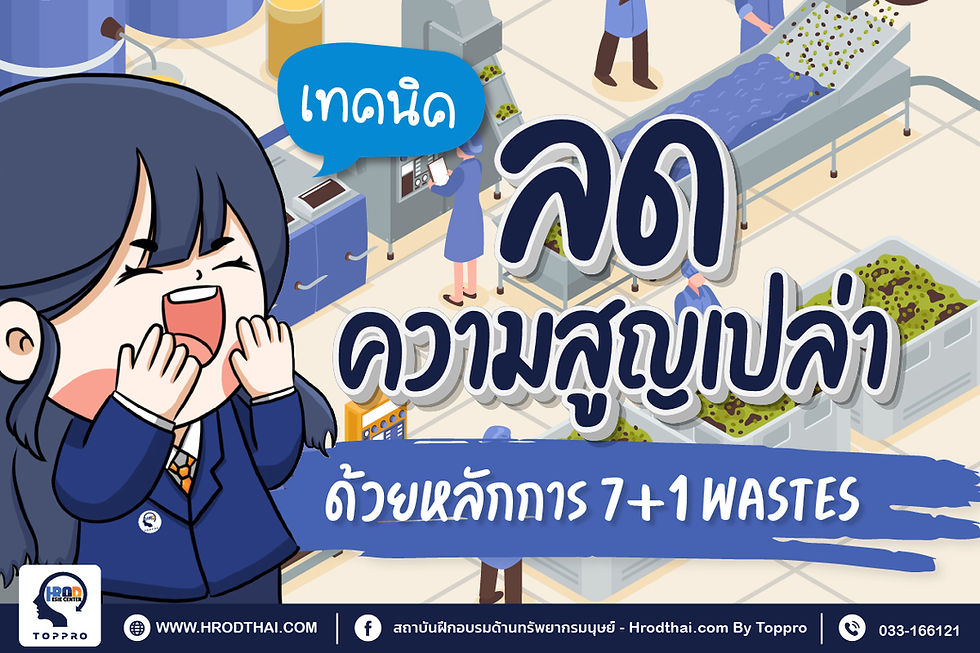
8 สูญเปล่าหรือ 8 Wastes เป็นแนวคิดทางการผลิตและการบริหารคุณภาพ ซึ่งมาจากกระบวนการการผลิตญี่ปุ่น โดยมีเป้าหมายเพื่อลดการสูญเปล่าและเพิ่มประสิทธิภาพในการผลิต 8 สูญเปล่าประกอบไปด้วย
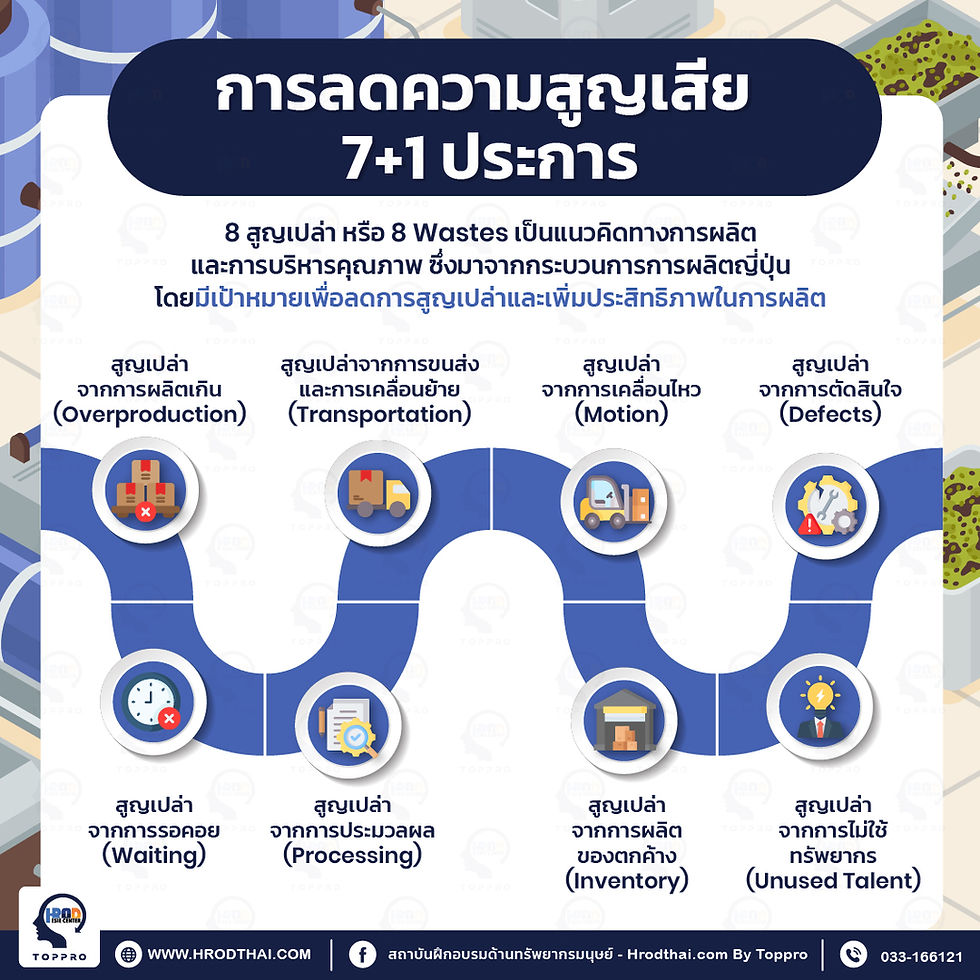
สูญเปล่าจากการผลิตเกิน (Overproduction) - การผลิตเกินกว่าที่ต้องการหรือไม่ได้รับคำสั่งซื้อจริงๆ ทำให้เกิดการสะสมวัตถุดิบ สินค้าสำเร็จรูปและขยะ มีผลให้เกิดค่าใช้จ่ายเพิ่มขึ้นและเสียโอกาสในการขายสินค้า
สูญเปล่าจากการรอคอย (Waiting) - การที่สินค้าหรือวัตถุดิบต้องรอในแต่ละขั้นตอนของกระบวนการผลิต ทำให้เวลาการผลิตเพิ่มขึ้น และเกิดค่าใช้จ่ายเพิ่มขึ้น
สูญเปล่าจากการขนส่งและการเคลื่อนย้าย (Transportation) - การเคลื่อนย้ายสินค้าหรือวัตถุดิบที่ไม่จำเป็น ทำให้เกิดค่าใช้จ่ายเพิ่มขึ้นและเสียเวลา
สูญเปล่าจากการประมวลผล (Processing) - การทำงานที่ไม่จำเป็นหรือซ้ำซ้อนในกระบวนการผลิต ทำให้เสียเวลา และเกิดค่าใช้จ่ายเพิ่มขึ้น
สูญเปล่าจากการเคลื่อนไหว (Motion) - การเคลื่อนไหวของเครื่องจักร อุปกรณ์ หรือบุคคลที่ไม่จำเป็นในกระบวนการผลิตทำให้เกิดค่าใช้จ่ายเพิ่มขึ้น และเสียเวลา
สูญเปล่าจากการผลิตของตกค้าง (Inventory) - การสะสมสินค้าสำเร็จรูปหรือวัตถุดิบเกินจำเป็นทำให้เสียค่าใช้จ่ายในการจัดเก็บ ความเสี่ยงในการเสียสินค้า และเสียโอกาสในการขายสินค้า
สูญเปล่าจากการตัดสินใจ (Defects) - การผลิตสินค้าที่ไม่ได้มาตรฐานหรือมีตำแหน่งที่ไม่ถูกต้อง ทำให้เกิดค่าใช้จ่ายในการแก้ไข และเสียโอกาสในการขายสินค้า
สูญเปล่าจากการไม่ใช้ทรัพยากร (Unused Talent) - ไม่ใช้ศักยภาพของพนักงานที่เกี่ยวข้องกับการผลิตทำให้เสียโอกาสในการพัฒนาทรัพยากรมนุษย์และประสิทธิภาพในการผลิต
การลด 8 สูญเปล่า เป็นวิธีที่มีประสิทธิภาพในการเพิ่มผลิตภาพ ลดต้นทุน และเพิ่มประสิทธิภาพในการจัดการทรัพยากรขององค์กร โดยการวิเคราะห์และปรับปรุงกระบวนการผลิตทุกขั้นตอน การปรับปรุงการจัดการทรัพยากรมนุษย์และการสร้างสภาพแวดล้อมที่เหมาะสมสำหรับการผลิต ในที่สุดจะช่วยให้ธุรกิจเพิ่มประสิทธิภาพและเพิ่มกำไรได้มากขึ้น
นอกจากนี้ การลด 8 สูญเปล่ายังช่วยให้องค์กรเป็นมิตรกับสิ่งแวดล้อมมากขึ้น เนื่องจากลดปริมาณการใช้ทรัพยากรไม่จำเป็น และลดปริมาณขยะที่เกิดขึ้นจากกระบวนการผลิต นอกจากนี้การลด 8 สูญเปล่ายังช่วยเพิ่มคุณภาพชีวิตของพนักงานด้วยการเพิ่มประสิทธิภาพในการทำงาน ลดความเครียด และเพิ่มความมั่นคงในงาน
สุดท้าย การลด 8 สูญเปล่าไม่ใช่เพียงแค่หน้าที่ของทีมผู้บริหารแต่เป็นหน้าที่ของทุกคนในองค์กร การทำงานร่วมกันในการลด 8 สูญเปล่าจะช่วยเพิ่มประสิทธิภาพในการผลิตและเพิ่มความมั่นคงของธุรกิจในระยะยาว
ต้นทุน หมายถึงอะไรบ้าง ?
ต้นทุนหมายถึงจำนวนเงินที่ใช้ในการผลิตหรือจัดหาสินค้าหรือบริการใดๆ เพื่อให้เกิดการผลิตหรือให้บริการนั้นเกิดขึ้นได้ โดยส่วนใหญ่แล้วต้นทุนจะประกอบด้วยสามส่วนหลัก ๆ คือ
ค่าใช้จ่ายในการจัดหาวัตถุดิบและวัสดุอุปกรณ์ที่ใช้ในการผลิต
ค่าใช้จ่ายในการจ้างแรงงาน
ค่าใช้จ่ายในการจัดหาและใช้เทคโนโลยี อุปกรณ์ และเครื่องมือต่าง ๆ ที่เกี่ยวข้องกับการผลิตหรือให้บริการ
นอกจากนี้ยังมีต้นทุนอื่น ๆ เช่น ค่าใช้จ่ายในการจัดการ ค่าใช้จ่ายในการขนส่ง ค่าใช้จ่ายในการตลาดและโฆษณา และค่าใช้จ่ายในการบริหารจัดการและกำกับดูแลธุรกิจ ซึ่งทั้งหมดนี้จะนำมาเป็นต้นทุนทั้งหมดของธุรกิจหรือผลิตภัณฑ์/บริการนั้น ๆ ซึ่งจะถูกนำมาคำนวณ ราคาขายหรือการกำหนดกำไรของธุรกิจนั้น ๆ โดยจะต้องใช้วิธีการคำนวณต้นทุนที่เหมาะสมกับธุรกิจ หรือกิจการนั้น ๆ ด้วยความสำคัญ เพื่อที่จะเป็นการบริหารจัดการที่มีประสิทธิภาพและกำไรมากที่สุด
หัวใจสำคัญของการควบคุมต้นทุนการผลิต
หัวใจสำคัญของการควบคุมต้นทุนการผลิต คือ การกำจัดกิจกรรมต่าง ๆ ที่ไม่มี หรือไม่ได้สร้างคุณค่าเพิ่มให้แก่ธุรกิจองค์กรนั่นเอง

หัวใจสำคัญของการควบคุมต้นทุนการผลิตคือการสร้างและบริหารจัดการกระบวนการผลิตให้มีประสิทธิภาพสูงสุดโดยลดต้นทุนให้ได้มากที่สุด โดยใช้หลักการควบคุมคุณภาพ และการวิเคราะห์ข้อมูลเพื่อเลือกวิธีการผลิตที่เหมาะสมที่สุด โดยหัวใจสำคัญที่สุดคือการวางแผนและการควบคุมการใช้ทรัพยากรให้มีประสิทธิภาพสูงสุด รวมถึงการพัฒนาและเลือกใช้เทคโนโลยีและอุปกรณ์ที่มีคุณภาพและราคาเหมาะสม อีกทั้งยังต้องพิจารณาเรื่องการจัดการความเสี่ยง เช่น ความเสี่ยงในการเกิดเหตุอุบัติเหตุในกระบวนการผลิต เพื่อลดต้นทุนการผลิตที่มีความเสี่ยงน้อยที่สุด ในที่สุดการควบคุมต้นทุนการผลิตนั้นเป็นเครื่องมือที่ช่วยให้บริษัทสามารถลดต้นทุนในการผลิตได้ จึงเป็นสิ่งสำคัญที่สุดในการบริหารจัดการธุรกิจ
จุดตรวจสอบ 5 M 1 E เพื่อการปรับปรุงควบคุมต้นทุนและลดการสูญเปล่าในการทำงาน
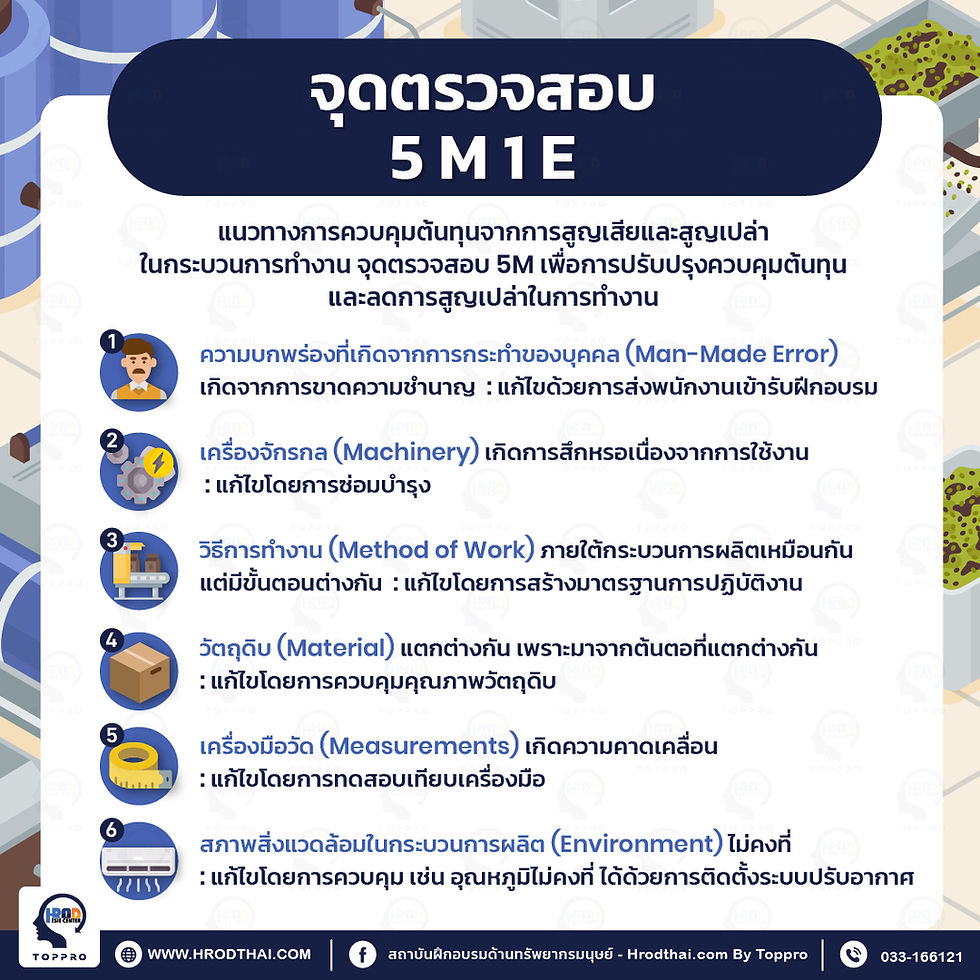
1. ความบกพร่องที่เกิดจากการกระทำของบุคคล (Man-Made Error) เกิดจากการขาด
ความชำนาญ : แก้ไขความบกพร่องด้วยการส่งพนักงานเข้ารับฝีกอบรม
2. เครื่องจักรกล (Machinery) เกิดการสึกหรอเนื่องจากการใช้งาน : แก้ไขโดยการซ่อมบำรุง
3. วิธีการทำงาน (Method of Work) ภายใต้กระบวนการผลิตเหมือนกัน แต่มีขั้นตอน
การปฏิบัติงานต่างกัน : แก้ไขโดยการสร้างมาตรฐานการปฏิบัติงาน
4. วัตถุดิบ (Material) แตกต่างกัน เพราะมาจากต้นตอที่แตกต่างกัน : แก้ไขโดยการ
ควบคุมคุณภาพวัตถุดิบ
5. เครื่องมือวัด (Measurements) เกิดความคาดเคลื่อน : แก้ไขโดยการทดสอบเทียบเครื่องมือ
6. สภาพสิ่งแวดล้อมในกระบวนการผลิต (Environment) ไม่คงที่ : แก้ไขโดยการควบคุม
เช่น อุณหภูมิไม่คงที่ : แก้ไขได้ด้วยการติดตั้งระบบปรับอากาศ หรือความชื่นสูง : แก้ไขด้วย
การติดตั้งเครื่องควบคุมความชื้น เป็นต้น
แนวคิดและแนวทางการควบคุมการลดต้นทุนการผลิต
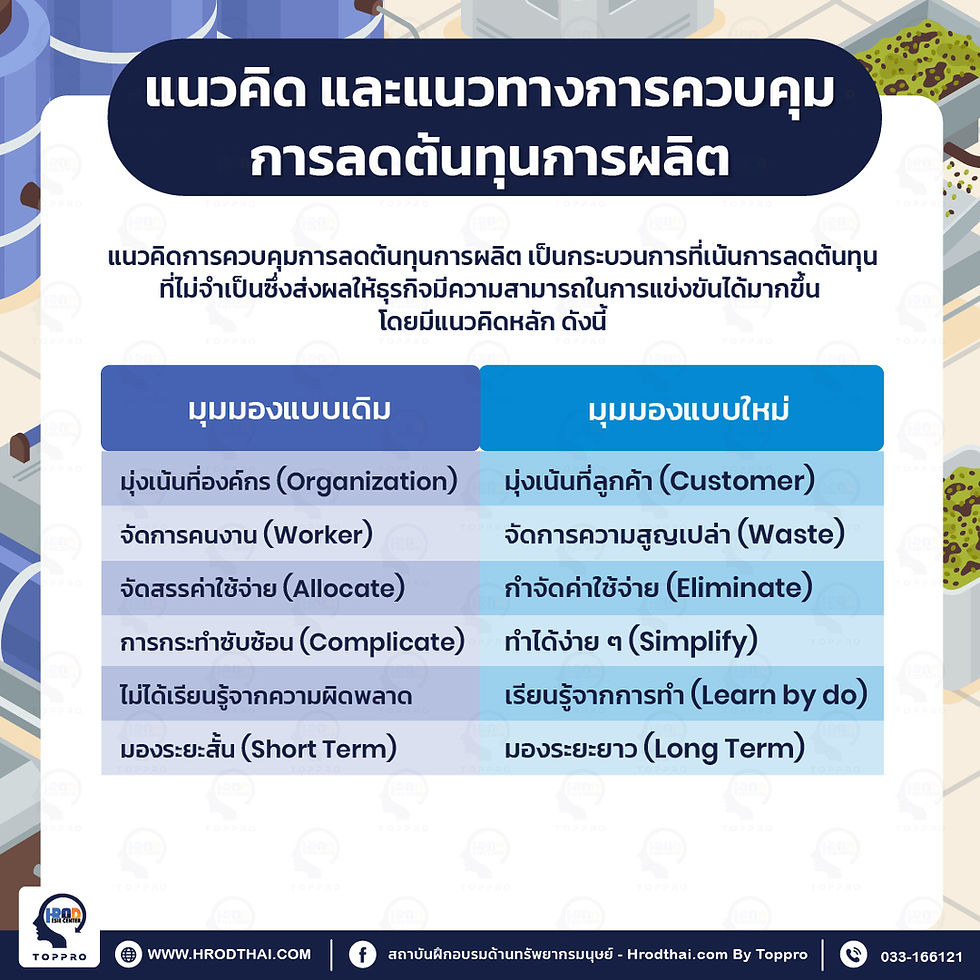
มุมมองแบบเดิม
มุ่งเน้นที่องค์กร (Organization)
จัดการคนงาน (Worker)
จัดสรรค่าใช้จ่าย (Allocate)
การกระทำซับซ้อน (Complicate)
ไม่ได้เรียนรู้จากความผิดพลาด
มองระยะสั้น (Short Term)
มุมมองแบบใหม่
มุ่งเน้นที่ลูกค้า (Customer)
จัดการความสูญเปล่า (Waste)
กำจัดค่าใช้จ่าย (Eliminate)
ทำได้ง่าย ๆ (Simplify)
เรียนรู้จากการทำ (Learn by do)
มองระยะยาว (Long Term)
วิธีมองและค้นหาปัญหาจาก QCDSMEE
QCDSMEE คือตัวอักษรย่อที่ใช้ในการวิเคราะห์ปัญหาในกระบวนการผลิต โดยประกอบด้วย
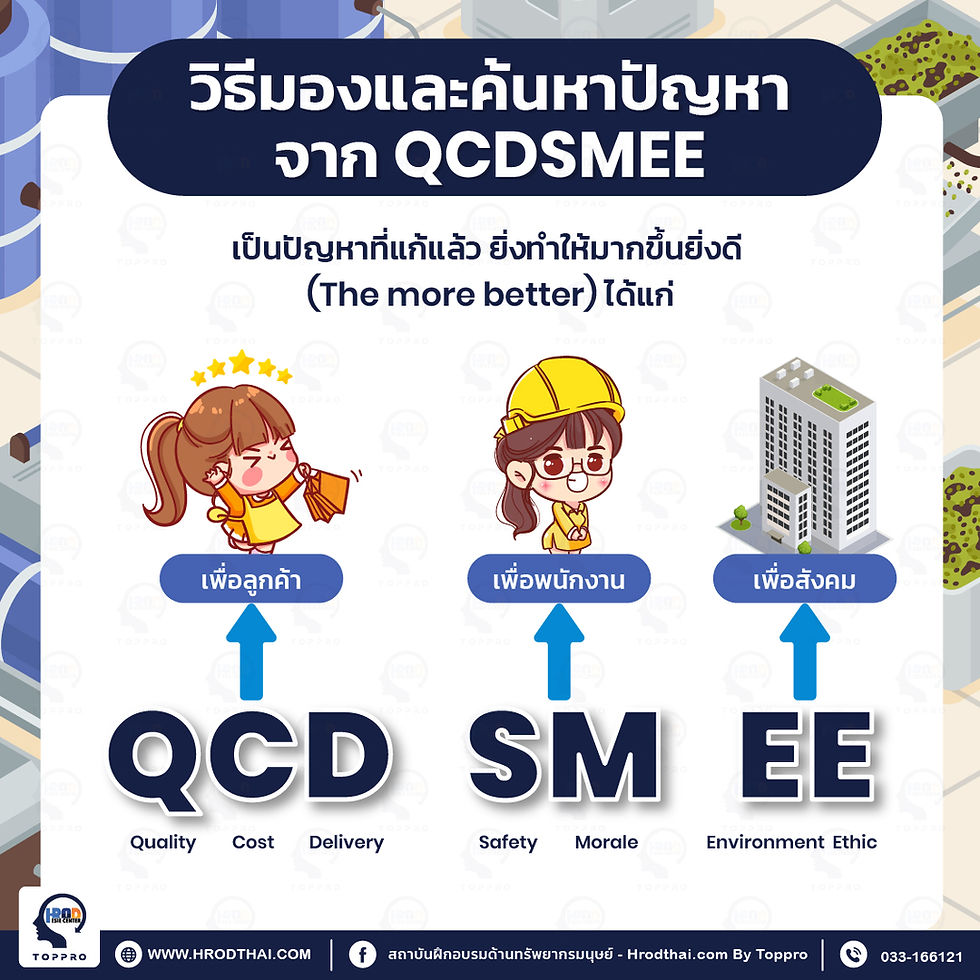
Q - Quality (คุณภาพสินค้า)
C - Cost (ต้นทุน)
D - Delivery (การส่งมอบสินค้า)
S - Safety (ความปลอดภัย)
M - Morale (ความสุขภาพของทีมงาน)
E - Environment (สิ่งแวดล้อม)
E - Equipment (อุปกรณ์)
วิธีการมองและค้นหาปัญหาจาก QCDSMEE มีดังนี้
วิเคราะห์ข้อมูล: รวบรวมข้อมูลทั้งหมดเกี่ยวกับกระบวนการผลิต ในแต่ละด้าน QCDSMEE และวิเคราะห์เพื่อหาปัญหา
สร้างแผนภาพกระบวนการ: สร้างแผนภาพกระบวนการที่ชัดเจนเพื่อเป็นเครื่องมือช่วยในการวิเคราะห์และประเมินปัญหา
พิจารณาความสำคัญ: ประเมินความสำคัญของปัญหาที่พบในแต่ละด้าน QCDSMEE โดยใช้เกณฑ์ต่าง ๆ เช่น ผลกระทบต่อลูกค้า ผลกระทบต่อต้นทุน และผลกระทบต่อความปลอดภัย
วิเคราะห์สาเหตุของปัญหา: ใช้เทคนิคต่าง ๆ เช่น Fishbone Diagram หรือ 5 Whys เพื่อหาสาเหตุของปัญหา
หาวิธีแก้ไขปัญหา: หลังจากพบปัญหาแล้ว ต้องคิดวิธีแก้ไขเพื่อลดผลกระทบต่อ QCDSMEE โดยเลือกวิธีที่เหมาะสมที่สุด
ดำเนินการแก้ไข: สร้างแผนการดำเนินการแก้ไขโดยใช้วิธีที่ได้รับการเลือกไว้ และนำไปปฏิบัติตามแผนการ โดยทีมงานจะต้องเข้าใจและร่วมมือกันในการแก้ไขปัญหา
ประเมินผล: หลังจากดำเนินการแก้ไขปัญหาแล้ว ต้องประเมินผลว่าการแก้ไขปัญหามีผลลัพธ์อย่างไร และสามารถสอดคล้องกับเป้าหมาย QCDSMEE หรือไม่
ติดตามและปรับปรุง: ติดตามผลการแก้ไขปัญหาเพื่อความแน่ใจว่าปัญหาจะไม่กลับมาเกิดซ้ำ และทำการปรับปรุงกระบวนการเพื่อเพิ่มประสิทธิภาพในอนาคต
สรุปว่า วิธีการมองและค้นหาปัญหาจาก QCDSMEE นั้นเป็นกระบวนการที่ช่วยให้ทีมงานสามารถวิเคราะห์ปัญหาในกระบวนการผลิตได้อย่างมีประสิทธิภาพ และทำการแก้ไขปัญหาอย่างมีประสิทธิภาพเพื่อลดความสูญเสียและเพิ่มประสิทธิภาพในกระบวนการผลิตให้เหมาะสม และมีคุณภาพขึ้น
การลดต้นทุนด้วยหลักการ 5 M
M1 – Man
M2 - Money
M3 - Machine
M4 - Material
M5 - Management

การลดต้นทุนด้วยหลักการ 5 M เป็นวิธีการที่ใช้ในการจัดการธุรกิจให้มีประสิทธิภาพและลดต้นทุนในการผลิต โดยหลักการ 5 M ประกอบด้วย
Man (มนุษย์) : การลดต้นทุนโดยการเพิ่มประสิทธิภาพของแรงงาน รวมถึงการเลือกใช้แรงงานที่มีความสามารถและความเชี่ยวชาญในงานที่ทำ
Money (เงิน) : การลดต้นทุนโดยการจัดการเงินอย่างมีประสิทธิภาพ เช่น การตรวจสอบรายการค่าใช้จ่าย การลดค่าใช้จ่ายในการจัดซื้อวัตถุดิบ การเลือกใช้วิธีการผลิตที่มีต้นทุนต่ำ
Machine (เครื่องจักร) : การลดต้นทุนโดยการเลือกใช้เครื่องจักรที่มีประสิทธิภาพและมีคุณภาพสูง เพื่อลดการเสียหายของเครื่องจักรและเพิ่มประสิทธิภาพในการผลิต
Material (วัตถุดิบ) : การลดต้นทุนโดยการเลือกใช้วัตถุดิบที่มีคุณภาพสูงและราคาถูก เพื่อลดต้นทุนในการผลิตและเพิ่มประสิทธิภาพในการผลิต
Management (การบริหาร) : การลดต้นทุนโดยการปรับปรุงการบริหารจัดการและกระบวนการผลิต เพื่อเพิ่มประสิทธิภาพในการผลิต รวมถึงการลดต้นทุนในการจัดหาเงินทุนหรือการกู้ยืมเพื่อเพิ่มสภาพคล่องในการจัดการ
นอกเหนือจากการลดต้นทุนด้วยหลักการ 5 M แล้ว การเพิ่มประสิทธิภาพในกระบวนการผลิตก็ถือ
เป็นการเพิ่มผลผลิตอีกทางหนึ่ง ซึ่งการเพิ่มประสิทธิภาพในกระบวนการผลิตนั้น สามารถทำได้ 5 วิธี ได้แก่
ผลผลิตเพิ่มโดยใช้ปัจจัยการผลิตเท่าเดิม (Output เพิ่มขึ้น Input เท่าเดิม)
ผลผลิตเพิ่มและปัจจัยการผลิตลดลง (Output เพิ่มขึ้น Input ลดลง)
ผลผลิตเพิ่มขึ้นมากกว่าปัจจัยการผลิตที่เพิ่มขึ้น (Output เพิ่มขึ้น Input เพิ่มน้อยกว่า)
ผลผลิตเท่าเดิมแต่ปัจจัยการผลิตลดลง (Output คงที่ Input น้อยลง)
ผลผลิตลดลงน้อยกว่าปัจจัยการผลิตที่ลดลง (Output ลด ลง Input ลดมากกว่า)
สำหรับเทคนิคต่างๆ ดังกล่าวข้างต้น เป็นหนึ่งในหลายๆ เครื่องมือที่สามารถนำมาวิเคราะห์ เพื่อหาแนวทางในการเพิ่มประสิทธิภาพของผลผลิต และเป็นส่วนหนึ่งที่ทำให้กระบวนการผลิตสามารถลดต้นทุนลงได้ ไม่มากก็น้อย อย่างไรก็ตาม การนำเทคนิควิธีดังกล่าวข้างต้นไปประยุกต์ใช้ จำเป็นต้องมีความรู้ ความเข้าใจในกระบวนการผลิตเป็นอย่างดี
แม้ว่าท้ายที่สุดแล้ว การเพิ่มผลผลิตนั้นถือเป็นหน้าที่ความรับผิดชอบที่ทุกคนต้องมีส่วนร่วมก็ตาม เพราะไม่ว่าจะเป็นการลดต้นทุน หรือการเพิ่มผลผลิต ก็ล้วนแต่เป็นกุญแจสู่ความสำเร็จทั้งสิ้น
Comments