การวิเคราะห์ข้อบกพร่องและผลกระทบ FMEA
การวิเคราะห์ข้อบกพร่องและผลกระทบ FMEA
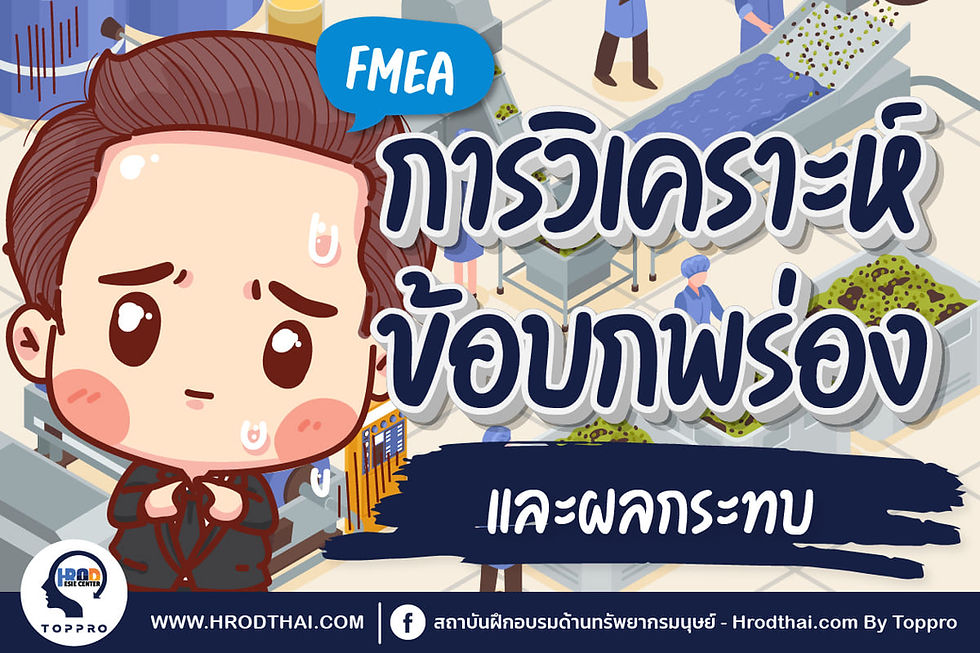
ในโลกแห่งการแข่งขัน องค์กรต่างพัฒนา และยกระดับคุณภาพสินค้าอย่างต่อเนื่องเพื่อให้ตรงกับความต้องการ และตอบสนองต่อความพึงพอใจของลูกค้า การควบคุมคุณภาพ จึงเป็นหัวใจสำคัญที่จะทำให้องค์กรบรรลุถึงความต้องการของลูกค้าได้ การควบคุมคุณภาพ จึงเป็นอีกขั้นตอนหนึ่งที่สำคัญในการป้องกันปัญหา และความล้มเหลวในขั้นตอนการออกแบบผลิตภัณฑ์ และควบคุมกระบวนการ โดยการวิเคราะห์ข้อบกพร่องและผลกระทบ (Failure Mode and Effects Analysis) FMEA จึงเป็นเครื่องมือที่สำคัญในการช่วยให้องค์กรมีการเตรียมความพร้อมเพื่อการวิเคราะห์ข้อบกพร่องและผลกระทบอย่างมีประสิทธิผล
FMEA เป็นเครื่องมือที่ใช้สำหรับการวิเคราะห์ และป้องกันความเสี่ยงต่าง ๆ ที่อาจส่งผลกระทบให้ผลลัพธ์ของกระบวนการไม่เป็นไปตามเป้าหมาย หากมองในระดับ ที่ใกล้ตัวมากขึ้นการออกแบบกระบวนการที่ป้องกันความเสี่ยงโดยสมบูรณ์ ก็อาจนึกถึงสถานการณ์ ที่เมื่อเราไม่คาดเข็มขัดนิรภัยก็จะมีเสียงสัญญาณดังขึ้น ในรถยนต์ของเรา เพื่อเตือนให้เรารู้และรีบคาดเข็มขัดนิรภัย ระบบล็อคอัตโนมัติ เมื่อรถยนต์มีความเร็ว ถึงระดับที่กำหนดไว้ เพื่อป้องกันการลืมล็อครถยนต์ เป็นต้น FMEA จึงเป็นเครื่องมือที่มีประสิทธิภาพสูง ซึ่งสามารถนำมาปรับใช้ได้กับกระบวนการทุกประเภท และจริง ๆ แล้ว การวิเคราะห์ข้อบกพร่องและผลกระทบ (Failure Mode and Effects Analysis) FMEA ก็สามารถประยุกต์ใช้ได้ ทั้งในระดับกระบวนการ กระบวนการย่อย หรือระดับผลิตภัณฑ์ก็ได้ โดยใช้ได้ทั้งกระบวนการผลิตสินค้า หรือกระบวนการให้บริการก็ได้
ความหมายของ FMEA

FMEA คือการวิเคราะห์ความเสี่ยง และเทคนิคการลดข้อผิดพลาดที่คำนึงถึง 3 ประการ
ความรุนแรงของข้อผิดพลาดที่เกิดขึ้น
ความน่าจะเป็นของสาเหตุ ที่เป็นไปได้ของความผิดพลาด
ความน่าจะเป็นความผิดพลาด หรือสาเหตุของข้อผิดพลาด ก่อนที่จะมีสินค้า ที่ผิดพลาดถึงลูกค้า
FMEA มีจุดมุ่งหมายเพื่อ
รับรู้และประเมินแนวโน้มของข้อบกพร่องของผลิตภัณฑ์ / กระบวนการหนึ่ง และผลกระทบจากข้อบกพร่องดังกล่าว
การบ่งชีี้ถึงการปฏิบัติการที่สามารถกำจัด หรือลดโอกาสเกิดข้อบกพร่อง
การดำเนินการจัดทำกระบวนการทั้งหมดให้อยูในรูปเอกสาร
FMEA มี 3 ชนิด

1. DFMEA (Design FMEA) วิเคราะห์ด้านการออกแบบผลิตภัณฑ์ เช่น
- ระบบหล่อเย็นของรถยนต์, ระบบเบรก, คอมพิวเตอร์
2. PFMEA (Process FMEA) วิเคราะห์ด้านกระบวนการผลิต เช่น
- การฉีดพลาสติก , การปั๊ม , การเชื่อม , การประกอบ
3. SFMEA (Service FMEA) วิเคราะห์ด้านบริการ
FMEA เป็นกระบวนการที่เกิดจากการทำงานกลุ่ม
FMEA เป็นกระบวนการที่เกิดจากการทำงานกลุ่ม ผู้มีส่วนร่วมในกิจกรรม FMEA ผู้มีส่วนร่วมในกิจกรรม FMEA ซึ่งควรประกอบด้วยผู้ที่มีความรู้ความสามารถในด้านต่าง ๆ เข้ามาประกอบกันเพื่อหาแนวทางป้องกันข้อบกพร่องอันเกิดขึ้นได้ในอนาคต กลุ่มกิจกรรม FMEA อาจประกอบด้วย
Design Engincer
Process , Production Engineer
Test Engineer
Maintenance
Quality Assurance
Operators
ปัจจัยที่มีผลต่อความสำเร็จ FMEA

ปัจจัยที่มีผลต่อความสำเร็จ FMEA
ช่วงเวลาที่ต้องดำเนินการ (ก่อนที่เหตุการณ์จะเกิดขึ้น ไม่ใช่หลังจากเกิดขึ้นแล้ว)
การเลือกทีมงาน FMEA
ความรู้ ,ความเข้าใจในหลักการของ FMEA และพื้นฐานงาน
ข้อมูลที่ต้องใช้ในการวิเคราะห์
ศัพท์เฉพาะ
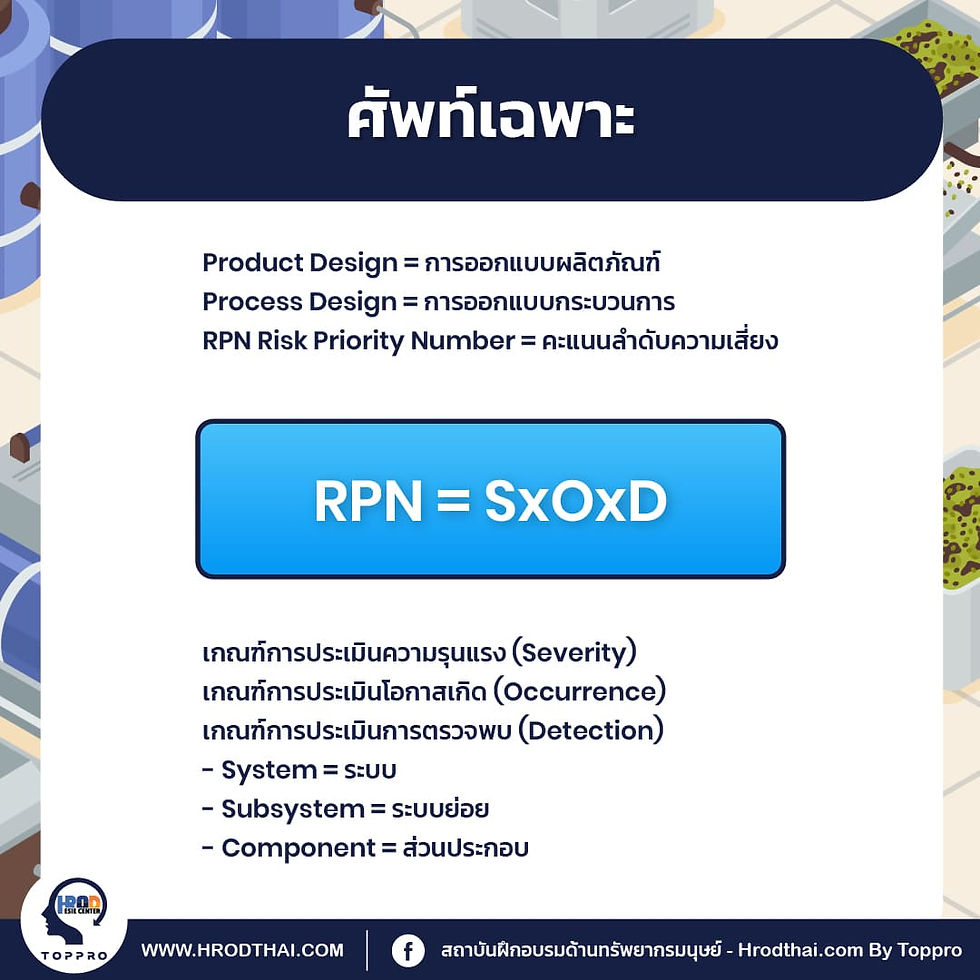
Product Design = การออกแบบผลิตภัณฑ์
Process Design = การออกแบบกระบวนการ
RPN Risk Priority Number = คะแนนลำดับความเสี่ยง
RPN = SxOxD
เกณฑ์การประเมินความรุนแรง (Severity)
เกณฑ์การประเมินโอกาสเกิด (Occurrence)
เกณฑ์การประเมินการตรวจพบ (Detection)
- System = ระบบ
- Subsystem = ระบบย่อย
- Component = ส่วนประกอบ
ตัวอย่างศึกษาลำดับขั้นตอนแต่ละกระบวนการ / การออกแบบ

ตัวอย่างการทำ FMEA อธิบายลักษณะของงาน
หรือหน้าที่ของแต่ละขั้นตอน
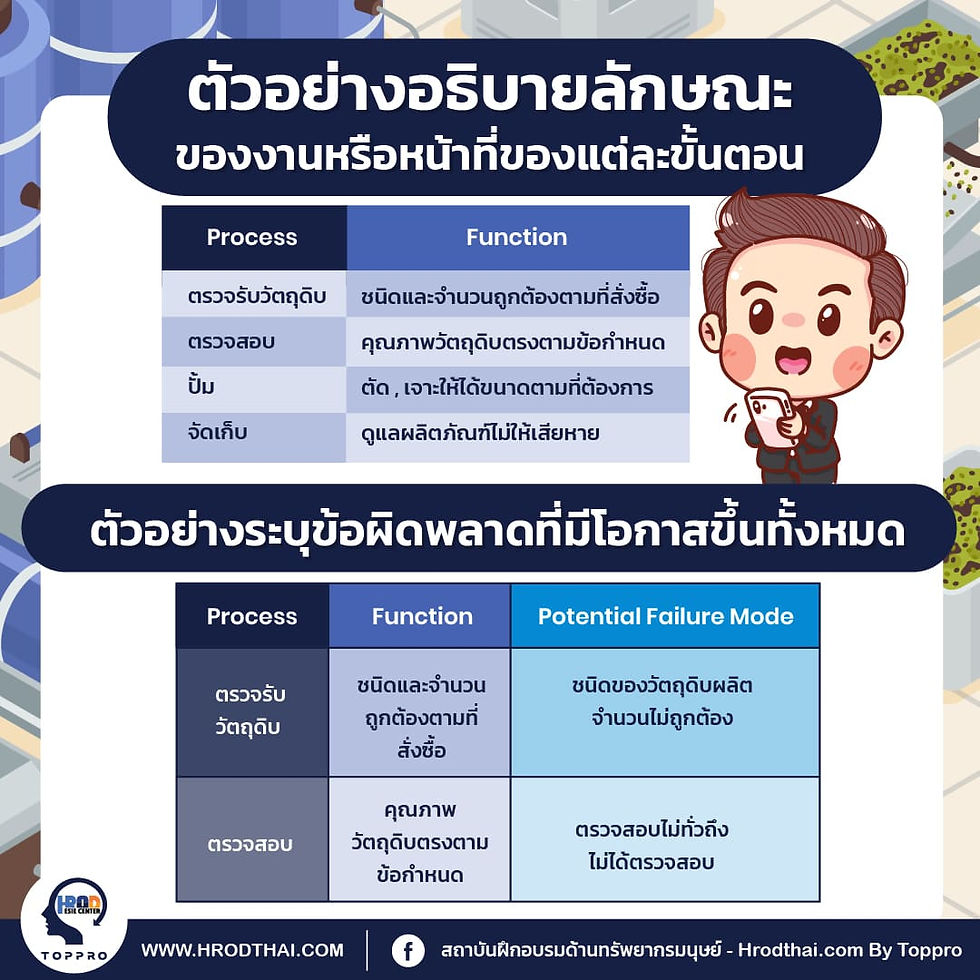
ตัวอย่างการทำ FMEA ระบุข้อผิดพลาดที่มีโอกาสขึ้นทั้งหมด
แสดงให้เห็นรูปแบบของความล้มเหลว ปัญหา และความผิดพลาดต่างๆ ที่อาจเกิดขึ้น หรือเกิดขึ้นแล้ว จากระบบงาน การออกแบบ การผลิตและการบริการ และมีการประเมินผล
อย่างไรก็ตาม FMEA ใช้สำหรับการออกแบบหรือปรับปรุงกระบวนการให้บรรลุผลสำเร็จ กล่าวคือเน้นในด้านประสิทธิผล (Effectiveness) ของกระบวนการเป็นหลัก แต่อาจไม่ได้คำนึงถึงในแง่ประสิทธิภาพ (Efficiency) ของกระบวนการมากนัก ดังนั้น หากท่านต้องการปรับปรุงกระบวนการให้ดีเลิศอย่างสมบูรณ์แบบไร้ที่ติ จึงยังคงจำเป็นต้องใช้เครื่องมืออื่น ๆ เข้ามาประกอบด้วยเพื่อทำให้กระบวนการปราศจากความสูญเปล่า ลดขั้นตอนที่ไม่เกิดมูลค่าเพิ่ม ซึ่งทำให้ต้นทุนต่าง ๆ ในการดำเนินการตามกระบวนการลดลง เมื่อนั้นจึงจะเกิด Excellence Process อย่างแท้จริง
Comentarios